Stainless Steel Surface Finish Guide
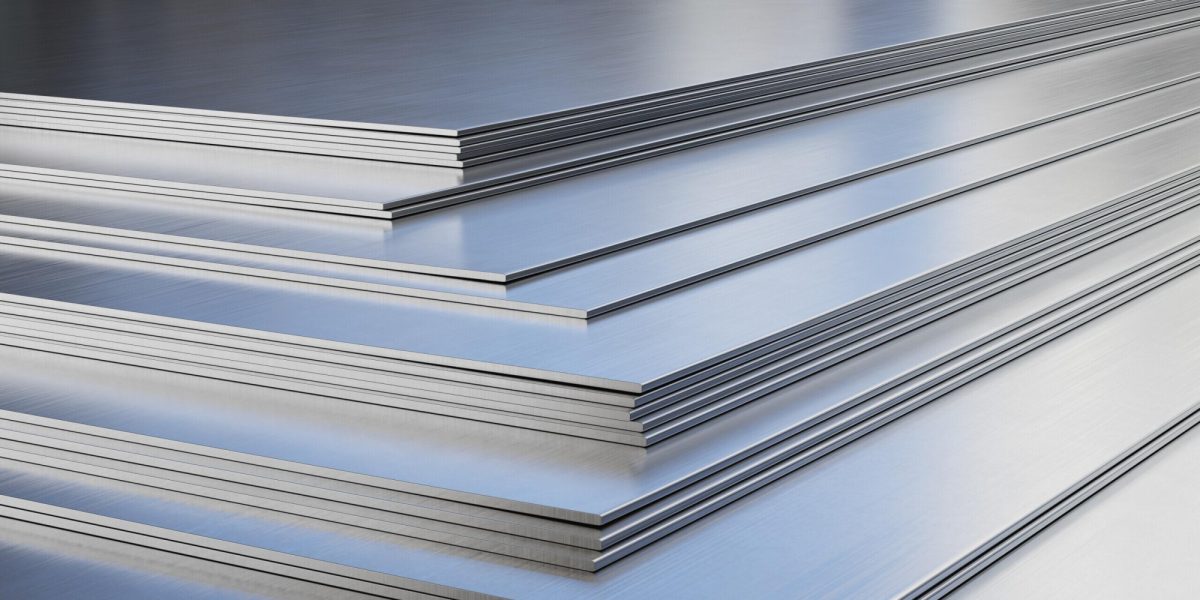
Explore mill and polished stainless steel surface finishes and how they impact formability, weldability, corrosion resistance, and appearance.
Why Surface Finish Matters
When sourcing stainless steel from a reliable stainless steel supplier, it's important to look beyond grade and gauge, and also consider the surface finish. The finish can:
- Influence formability and weldability
- Affect corrosion resistance
- Determine cleanability and hygienic compliance
- Add (or reduce) post-processing steps
- Impact cost and lead times
What Are Stainless Steel Finishes?
Stainless steel finishes are the result of specific production processes like rolling, annealing, pickling, polishing, or buffing. The finish affects not just the look of the material, but also how it behaves during fabrication – especially when bending, welding, or cleaning.
This guide breaks stainless finishes down into two main types: Mill Finishes (produced during initial processing) and Polished Finishes (mechanically refined for enhanced appearance or function). Understanding the differences and benefits of the most common stainless steel finishes helps you make smarter buying decisions – and avoid costly mistakes.
Mill Finishes
Mill finishes are exactly what they sound like – finishes as they are produced on the material direct from the mill. These are functional, cost-effective, and widely used in manufacturing.
1. No. 1 Finish – Rugged and Functional
- Production Process: Hot rolled, annealed, descaled (pickled).
- Appearance: Dull, rough, non-uniform matte.
- Typical Gauges: Heavier (above 3 mm)
- Use Cases: Pressure vessels, furnace parts, structural supports, boiler components.
- Manufacturing Considerations:
- Formability: Fair; rougher surface can affect tool wear.
- Weldability: Good; surface doesn’t interfere with welds.
- Post-Processing: Usually not visible, so minimal polishing.
- Corrosion Resistance: Excellent, especially for 304/316 grades.
Best for buyers who prioritize strength and corrosion resistance over aesthetics.
2. 2D Finish – Cold Rolled, Annealed, and Pickled
- Production Process: Cold rolled, annealed, pickled, no final pass.
- Appearance: Smooth but dull gray.
- Use Cases: Chemical equipment, structural parts, automotive exhaust components.
- Manufacturing Considerations:
- Formability: Better than No. 1; can be formed and drawn.
- Weldability: Good; not visually critical.
- Cost Efficiency: Budget-friendly for internal or hidden parts.
Best for internal components or functional parts not exposed to view.
3. 2B Finish – Matte, Smooth, and Machine-Friendly
- Production Process: Cold rolled, annealed, pickled, light skin pass with polished rolls.
- Appearance: Uniform, smooth, matte-gray sheen.
- Use Cases: Cabinets, tanks, HVAC systems, appliances.
- Manufacturing Considerations:
- Formability: Excellent; smooth surface aids stamping, rolling, and bending.
- Weldability: Seam blends well post-weld.
- Post-Processing: Can be painted or coated if needed.
Ideal for multi-use manufacturing where both performance and cost control matter.
4. BA (Bright Annealed) Finish – Reflective and Precision-Friendly
- Production Process: Cold rolled, annealed in a controlled atmosphere (no pickling).
- Appearance: Bright, reflective, smooth.
- Use Cases: Food processing equipment, automotive trim, cleanroom enclosures.
- Manufacturing Considerations:
- Formability: Excellent; smooth surface minimizes friction.
- Weldability: High, but weld discoloration may need cleaning.
- Corrosion Resistance: Slightly reduced due to smoother surface limiting passivation.
Ideal when formability and cleanliness are priorities, without full mirror cost.
Polished Finishes
Mechanically polished or buffed for enhanced aesthetics, functionality, or hygiene.
5. No. 3 Finish – Intermediate Polished (100–120 Grit)
- Production Process: 2B base polished with coarse abrasives.
- Appearance: Brushed with visible directional grain.
- Use Cases: Architectural interiors, elevator doors, low-visibility decorative items.
- Manufacturing Considerations:
- Formability: Moderate; avoid forming against grain.
- Post-Processing: Grain matching needed after welding or cutting.
Useful for semi-decorative applications where appearance matters but perfection isn't required.
6. No. 4 Finish – Standard Brushed (150–180 Grit)
- Production Process: 2B base polished with finer abrasives.
- Appearance: Satin, directional polish with smoother lines than No. 3.
- Use Cases: Commercial kitchens, medical equipment, architectural panels.
- Manufacturing Considerations:
- Formability: Good; grain direction matters in bending.
- Post-Weld Restoration: Requires polishing or grain re-blending.
- Hygiene: Preferred for food and medical due to cleanability.
A great balance of aesthetics, functionality, and cost.
7. No. 6 Finish – Fine Brushed (Buffed No. 4)
- Production Process: No. 4 finish followed by light buffing.
- Appearance: Duller than mirror, brighter than standard brushed.
- Use Cases: Cosmetic panels, architectural accents.
- Manufacturing Considerations:
- Formability: Moderate.
- Cleanability: Easy to maintain.
- Scratch Resistance: Better than high-gloss finishes.
Used when you need a soft glow rather than full reflection.
8. No. 7 Finish – Pre-Mirror Polish
- Production Process: Heavily buffed; some grit lines remain visible.
- Appearance: Very reflective with swirl marks.
- Use Cases: Commercial displays, trims, accents.
Intermediate step before full mirror polish.
9. No. 8 Finish – Mirror Finish
- Production Process: Repeated buffing of BA base to a flawless, reflective surface.
- Appearance: True mirror, no visible grit lines.
- Use Cases: Luxury architecture, retail fixtures, mirrors, elevator interiors.
- Manufacturing Considerations:
- Formability: Low; surface is easily scratched.
- Weldability: Challenging to restore.
- Packaging: Protective film required.
- Cost: Premium.
Chosen when aesthetics and prestige matter most.
Specialty & Custom Finishes
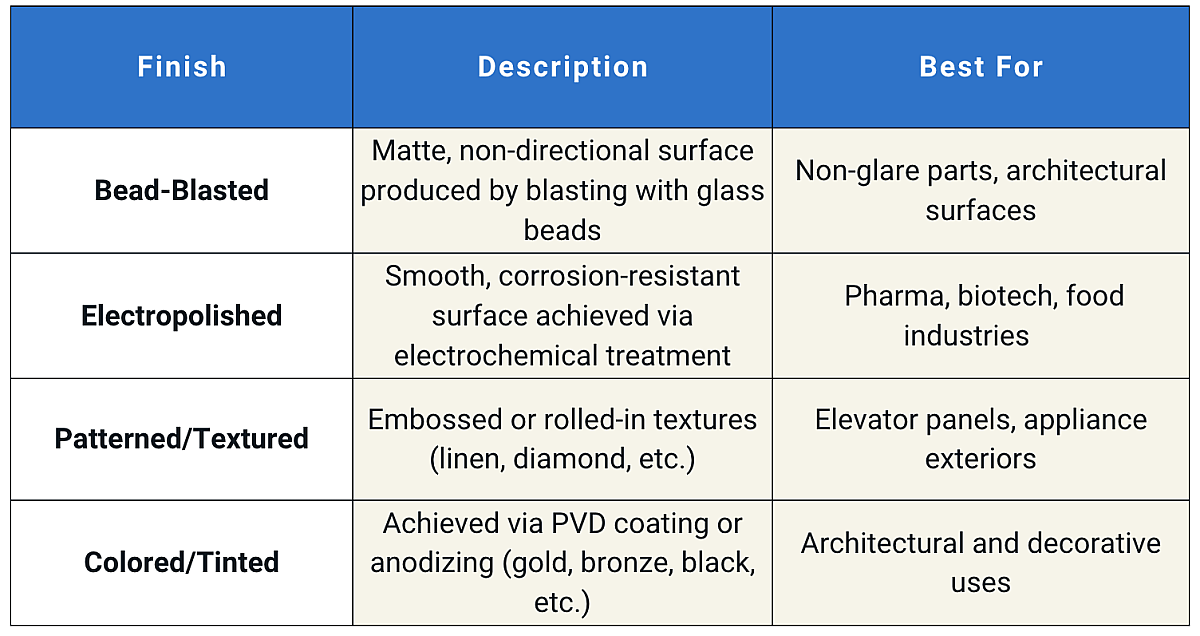
How to Choose the Right Finish for Your Application
Ask yourself these questions:
- Will the material be seen by end users?
- Does it need to withstand corrosive or sanitary environments?
- How much forming, cutting, or welding will be required?
- Is cost control or aesthetics your top priority?
The right surface finish can improve downstream performance and reduce finishing labor – ultimately saving time and money.
Mill Steel Company: Your Stainless Steel Coil Partner
As a national stainless steel supplier, Mill Steel stocks a full range of stainless steel coils in multiple finishes, widths and gauges. Whether you're fabricating architectural panels, kitchen equipment, or industrial enclosures, we’re here to support your project with:
- Custom slitting and packaging
- Nationwide delivery and just-in-time service
- Exceptional customer service and support
- Industry expertise to match finish to function
Need help selecting a finish or placing an order? Contact Mill Steel today to speak with a knowledgeable stainless steel expert, or conveniently shop our products online.