The Most Popular Aluminum Types and Grades
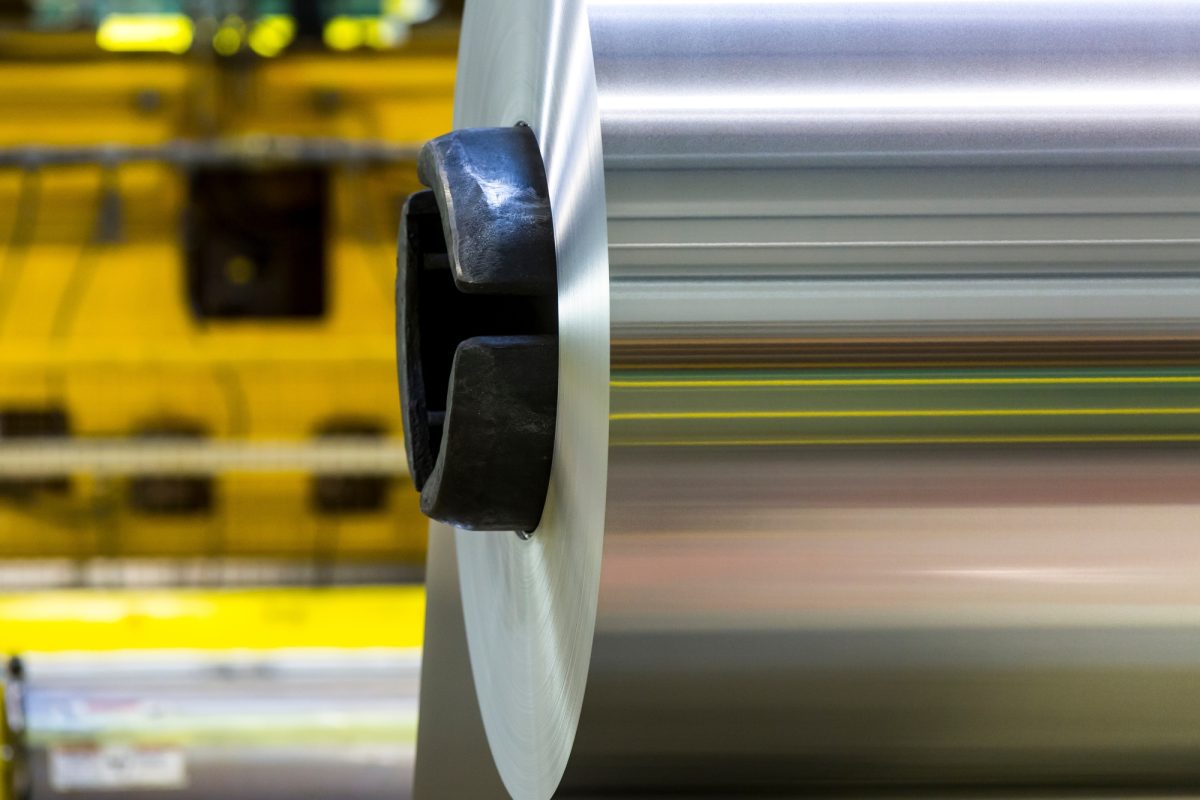
A Practical Guide for Buyers Working with Aluminum Alloys and Coil
Aluminum is one of the most widely used metals in the world, known for its strength-to-weight ratio, corrosion resistance, and workability. Whether used in construction, transportation, solar energy systems, or manufacturing, aluminum’s versatility lies in its various alloys and forms—each suited for different applications.
If you're sourcing material for fabrication or production, it’s important to understand both the differences between aluminum alloys and aluminum coil, and which grades are best for your needs. This guide outlines the most popular types and grades of aluminum, along with tips to help buyers make informed decisions.
Understanding the Basics: Aluminum Alloy vs. Aluminum Coil
What Are Aluminum Alloys?
An aluminum alloy is a composition of aluminum combined with other elements such as copper, magnesium, manganese, silicon, or zinc. These elements are added to enhance specific properties like strength, corrosion resistance, or formability.
Aluminum alloys fall into two broad categories:
- Wrought alloys – processed by mechanical working (rolling, extruding, etc.) and designated with a four-digit system (e.g., 3003, 5052).
- Within wrought alloys, there are two types:
- Non-heat-treatable alloys – gain strength through cold working (e.g., 3003, 5052)
- Heat-treatable alloys – gain strength through thermal processes (e.g., 6061, 2024)
- Within wrought alloys, there are two types:
- Cast alloys – formed by pouring molten metal into molds. These are less common in coil or sheet form.
What Is Aluminum Coil?
Aluminum coil is a rolled form of aluminum alloy, typically wound into large spools after being processed through hot or cold rolling mills. Coil is commonly used in:
- Roll forming and stamping
- HVAC ducting
- Building facades and gutters
- Automotive panels and fuel tanks
Coil is preferred when buyers require continuous lengths of material for high-efficiency processing or fabrication.
Common Types of Aluminum Coil
Aluminum coil can be produced in a variety of tempers and coatings. Some common types include:
- Mill finish aluminum coil – uncoated, natural aluminum surface
- Pre-painted aluminum coil – factory-applied paint or coating for aesthetic or corrosion-resistant applications
- Anodized aluminum coil – electrochemically treated for enhanced surface hardness and color
- Clad aluminum coil – layered with another metal or alloy for performance benefits (often used in brazing or heat exchanger applications)
Popular Aluminum Grades and Their Uses
Here’s a breakdown of widely used aluminum grades that are often stocked in coil or sheet form:
1000 Series (e.g., 1100)
- Pure aluminum (99% or higher). This is often called commercially pure aluminum.
- Excellent corrosion resistance and thermal conductivity, it can be welded using any method but is not heat-treatable
- Best for: Chemical equipment, electrical work, food processing, signage, lighting, and HVAC to name a few.
- Note: This is very soft, not suitable for structural applications
3003 Aluminum
- Aluminum-manganese alloy (non-heat-treatable), the most widely used of all aluminum alloys
- Good corrosion resistance, formability, and weldability. This grade can be deep drawn or spun, welded or brazed. It is non heat treatable.
- Best for: Roofing, siding, cookware, gutters, hardware, HVAC, pressure vessels, trailer and truck panels
- Tip: Often used with painted finishes due to its excellent coating adhesion.
3105 Aluminum
- Similar to 3003, but with slight additions for increased strength. It can be annealed during cold working.
- Best for: Residential siding, mobile homes, flashing, rain-carrying goods
5052 Aluminum
- Aluminum-magnesium alloy (non-heat-treatable)
- High strength and excellent corrosion resistance in marine environments
- Best for: Marine panels, fuel tanks, fans, fencing, truck trailers
- Tip: Performs well in saltwater and is commonly used for coastal construction.
5005 Aluminum
- Good for anodizing, similar to 5052 in corrosion resistance but lower strength
- Best for: Architectural applications requiring a high-quality anodized finish
6061 Aluminum
- Aluminum-magnesium-silicon alloy (heat-treatable), the least expensive and most versatile of the heat-treatable alloys.
- High strength, good weldability, and corrosion resistance. After heat treatment, it is considered equal to low carbon steel for strength.
- Best for: Structural components, truck frames, aerospace
- Tip: 6061 is often used when strength and machinability are critical.
8011 Aluminum
- Often used in foil and packaging applications
- Contains iron and silicon for improved strength
- Note: Not typically used in coil form for structural purposes.
How to Choose the Right Aluminum Alloy or Coil
Choosing the correct aluminum alloy or coil type depends on several factors:
- Application environment (indoor vs. outdoor, marine vs. industrial)
- Required strength and weight
- Forming or welding needs
- Finish requirements (painted, anodized, bare)
- Budget and availability
Additional Resources for Aluminum Buyers
- Aluminum Association Industry Standards & Chemical Compositions
- London Metal Exchange Aluminum Pricing
- MatWeb Material Property Database
Staying informed on alloy differences and market trends can help you optimize both sourcing strategy and material performance.
About Mill Steel Company
Mill Steel is a leading national steel and aluminum supplier, offering a wide variety of products across key industries including construction, transportation, and manufacturing. With extensive processing capabilities and a customer-first approach, Mill Steel supports manufacturers with consistent quality and responsive service.